Sand Molded Casting Foundry from China with OEM Custom Services and CNC Machining.
Casting is the process where metal is heated until molten. While in the molten or liquid state it is poured into a mold or vessel to create a desired shape. We have found that by carefully choosing alloys and applying proven methods of heat treatment, we can produce castings of high quality, strength and wearability. The casting process better lends itself to making parts where internal cavities are required.
Sand casting is often utilized in industry (automotive, aerospace, hydraulics, agricultural machinery, rail trains...etc.) to make parts that are comprised of iron, steel, bronze, brass and at times aluminum. The metal of choice is melted in a furnace and poured into a mold cavity formed out of sand. Sand casting is used because it is inexpensive and the process is relatively simple.
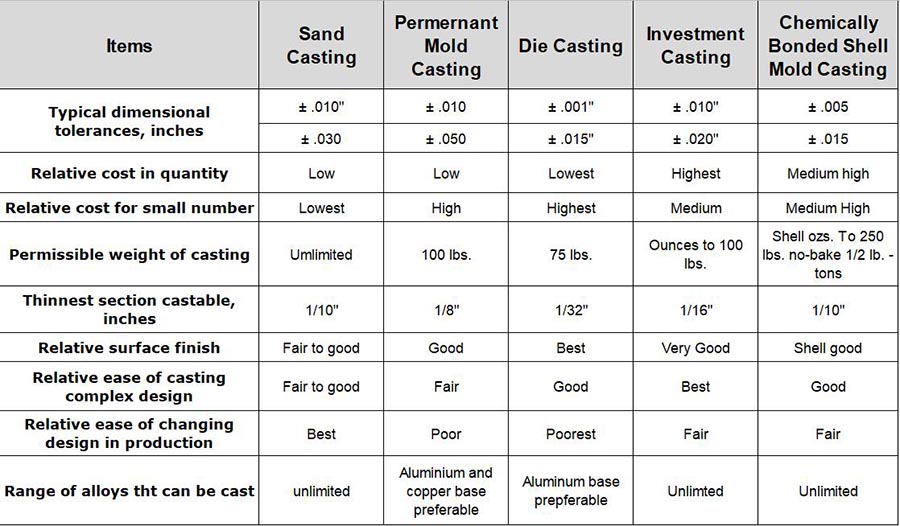
▶ Capabilities of Sand Casting moulded by hand:
• Max Size: 1,500 mm × 1000 mm × 500 mm
• Weight Range: 0.5 kg - 500 kg
• Annual Capacity: 5,000 tons - 6,000 tons
• Tolerances: On Request or Standard (ISO8062-2013 or Chinese Standard GB/T 6414-1999)
• Mold Materials: Green Sand Casting, Shell Mold Sand Casting.
▶ Capabilities of Sand Casting by Automatic Molding Machines:
• Max Size: 1,000 mm × 800 mm × 500 mm
• Weight Range: 0.5 kg - 500 kg
• Annual Capacity: 8,000 tons - 10,000 tons
• Tolerances: On Request or According to Standard (ISO8062-2013 or Chinese Standard GB/T 6414-1999)
• Mold Materials: Green Sand Casting, Resin Coated Sand Shell Molding Casting.
▶ Raw Materials Available for Sand Casting Foundry at RMC:
• Gray Iron: HT150, HT200, HT250, HT300, HT350; GJL-100, GJL-150, GJL-200, GJL-250, GJL-300, GJL-350; GG10~GG40.
• Ductile Iron or Nodular Iron: GGG40, GGG50, GGG60, GGG70, GGG80; GJS-400-18, GJS-40-15, GJS-450-10, GJS-500-7, GJS-600-3, GJS-700-2, GJS-800-2; QT400-18, QT450-10, QT500-7, QT600-3, QT700-2, QT800-2;
• White iron, compacted graphite iron and malleable iron.
• Aluminium and Their Alloys
• Brass, Red Copper, Bronze or other Copper-based metals
• Other Materials as per your unique requirements or according to ASTM, SAE, AISI, ACI, DIN, EN, ISO, and GB standards
▶ The Advantages of Casting Include:
• No real upper size limit in casting weight
• Large range of alloy choices
• Alloys including Chrome, Nickel and Moly can be added at the molten stage.
• Tooling is often less expensive than forge dies and othe casting methods.
• Smaller production "runs" required
• Complicated/complex parts are no problem
▶ What We Can Do For You?
• Do you currently fabricate iron/steel/alminium components for your machinery?
• Are you unhappy with the quality, price and leadtime of your current suppliers?
• Are the parts you are currently receiving inconsistent in quality and delivery
• Is your supplier an importer of parts (as opposed to the true manufacturer)
If you answered yes to any one of these questions give us a call or contact us. We will save you money. We guarantee your complete satisfaction with our parts and service. If you are unhappy with a part – we will sit down with you, work out the shortcomings and make the necessary changes until you are 100% satisfied
Quick Links:
Sand Casting | Investment Casting | CNC Machining | Lost Foam Casting | Vacuum Casting | Get a Quote