Sand casting process is a basic and important manufacturing procedure in metal forming industry. Here in this article we introduced some future trends of the sand casting process. The sand casting foundry is the companies who are proceeding this.
1 Foundry technology is developing towards energy saving and material saving
In the casting production process, a large amount of energy is consumed in the metal smelting process. At the same time, the demand for consumables in the sand casting process is also great. Therefore, how to better save energy and materials is a major issue facing sand casting plants. The commonly used measures mainly include:
1) Adopt advanced sand molding, core-making technology and equipment. In the sand casting production process, high pressure, static pressure, injection pressure and air punching equipment should be used as much as possible. And as far as possible to use self-hardening sand, lost foam casting, vacuum casting and special casting (such as investment casting, metal mold casting) and other technologies.
2) Sand recovery and reuse. When casting non-ferrous metal parts, iron castings and steel castings, according to the sintering temperature of the sand, the recovery rate of mechanically regenerated old sand can reach 90%. Among them, the combination of sand recycling and wet regeneration is the most ideal and cost-effective method.
3) Recycling of adhesives. For example, if the casting is de-cored by dry method and the adhesive remains in the sand, the appropriate process can make the adhesive be reused, thereby greatly reducing the cost of the adhesive.
4) Regeneration of molds and mold materials.
2 Less pollution or even no pollution
The sand casting foundry produces a lot of waste water, waste gas and dust during the production process. Therefore, the foundry is not only a large energy consuming household, but also a large pollution source. Especially in China, pollution in foundries is more serious than in other countries. Among them, the dust, air and solid waste discharged from sand casting plants are the most serious. Especially in recent years, China's environmental protection policies have become more and more stringent, and foundries have had to take effective measures to control pollution. To achieve green and clean production of sand casting, green inorganic binders should be used as much as possible, or less or no binders should be used. Among the sand casting processes currently involved, lost foam casting, V process casting and sodium silicate sand casting are relatively environmentally friendly. Because lost foam casting and V process casting use dry sand modeling that does not require binders, while sodium silicate sand casting uses organic binders.
3 Higher dimensional and geometrical accuracy of castings
With the development of the precision forming process of casting blanks, the gemometical and dimensional accuracy of part forming is developing from near net shape forming to net shape forminig, that is, almost no margin forming. The difference between the casting blank and the required parts is getting smaller and smaller. After some blanks are formed, they have approached or reached the final shape and size of the parts, and can be assembled directly after grinding.
4 Less or no defects
Another indicator of casting roughness and parts forming level is the number, size and damage of casting defects. Because the hot working and metal casting processes are very complicated and affected by many factors, casting defects are difficult to avoid. However, few or no defects are the future trend. There are several effective measures:
1) Adopt advanced technology to increase the density of alloy structure and lay the foundation for obtaining sound castings.
2) Use casting simulation software to simulate the actual casting process in the design stage in advance. According to the simulation results, the process design is optimized to realize the success of one-time molding and mold trial.
3) Strengthen the process monitoring and perform operations strictly in accordance with the determined operating instructions.
4) Strengthen non-destructive testing in the production process, find out-of-standard parts in time and take corresponding remedial and improvement measures.
5) Determine the critical defect value through the research and evaluation of the safety and reliability of the parts.
5 Lightweight production of castings.
In the production of passenger cars, trucks, and other transportation equipment, how to minimize the weight of parts while ensuring the strength of the parts is an increasingly obvious trend. There are two main aspects to achieve weight reduction. One is to use light raw materials, and the other is to reduce the weight of parts from the structural design of the parts. Because sand castings have great flexibility in structural design, and there are also many traditional and new metal materials to choose from, sand casting can play a huge role in lightweight production.
6 Application of new technologies such as 3D printing in mold making
With the development and maturity of 3D printing technology, it is also more and more widely used in the casting field. Compared with traditional mold development, 3D printing technology can quickly produce the required molds at a lower cost. As a rapid prototyping technology, 3D printing can give full play to its advantages in the sample trial production and small batch stages of castings.
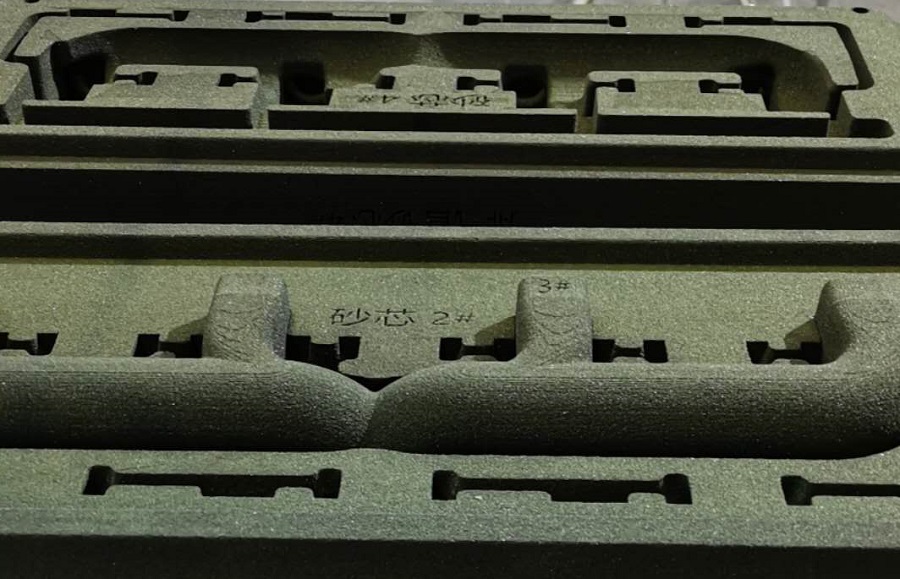
A 3D Printing Sand Molding